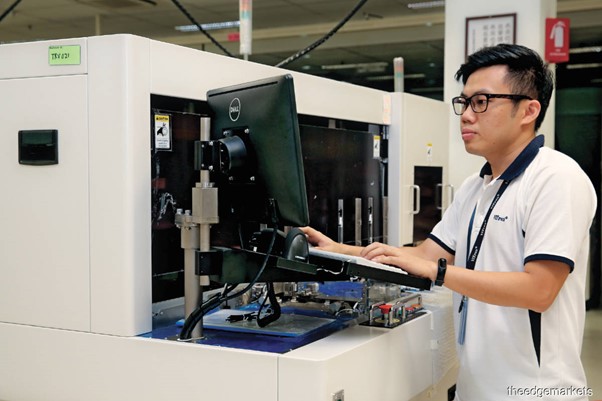
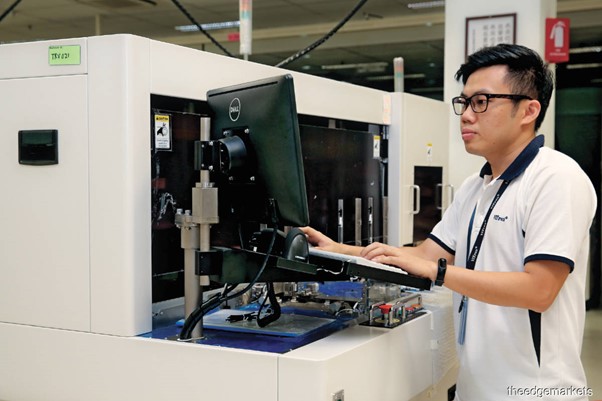
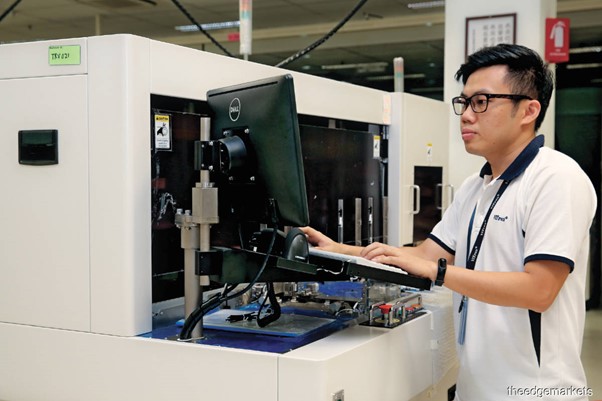
In layman’s terms, automated test equipment (ATE) systems are designed to not only reduce the amount of test time needed to verify that a particular semiconductor device or high-tech gear works, but also to prevent the defective ones from reaching end-users.
As investors focus on environmental, social and governance (ESG) practices adopted by investee companies these days, will ATE companies gain traction, considering that their equipment could help reduce electronic waste (e-waste)?
ViTrox Corp Bhd CEO and president Chu Jenn Weng believes so. “If our machine does not discover the abnormality in our customers’ production lines, then these defective materials will be used in the next level of production, and the end products won’t be able to function. But if we discover [the defects] earlier, then we could alert our customers to halt and revoke production, so that they don’t continue producing something that cannot be used. So, our ATE products play an important role in reducing e-waste,” he explains.
Batu Kawan-headquartered ViTrox provides machine vision system (MVS) and automated board inspection solutions for integrated device manufacturers such as outsourced semiconductor assembly and test (OSAT) and electronic manufacturing services (EMS) players.
Chu, who co-founded ViTrox in 2000, and is now the 35th richest man in Malaysia, says e-waste is mostly copper and gold, which are natural resources. “Imagine, there is a lot of work done to extract all these natural minerals. Therefore, we should help our customers reduce wastage as much as we can. Without ATE and MVS, can you imagine how much e-waste there will be every day?”
He acknowledges that realistically, ATE companies cannot stop their immediate clients from producing more semiconductors or electronic goods for end-customers. However, the ATE firms could help them significantly reduce e-waste in the manufacturing processes by detecting all the defects as early as possible by using the MVS solution.
“Defects and discrepancies can be detected early when it happens and hence stopped from producing more in the manufacturing process, if they can be spotted and resolved earlier,” says Chu.
From a broader perspective, he points out that Malaysia is in a sweet spot amid the US-China trade war, and local ATE firms could be beneficiaries. “Regardless of the outcome, both China and the US could source the equipment from us. We have the capability to meet their requirements. China is building its own semiconductor ecosystem, so it is buying a lot of wafer fab equipment and back-end semiconductor equipment.”
With Malaysian-made equipment, Industrial Revolution 4.0 solutions, artificial intelligence and a strong local supply chain ecosystem, multinational corporations will soon realise that they can make their products in a more cost-effective manner and be less dependent on migrant workers, says Chu.
“We have the technology to export to the world. We have the cost advantages over advanced countries such as Japan and Taiwan. I would say Malaysia is quite strong in the area of back-end semiconductor testing equipment. Overall, we just need to improve our R&D and marketing,” he adds.
Source: Edge Weekly